Skeleton oil seal, standard name rotary shaft lip seal, is referred to as an oil seal, and because of the spring, it is also known as a self-tightening oil seal. The main function of the oil seal is to isolate the parts that need lubrication in the transmission parts from the external environment so that the lubricating oil or grease does not leak out, to maintain the continuous lubrication of the transmission structure. The structure of the skeleton oil seal is diverse, and there are many kinds of materials. The main function is to prevent oil leakage inside and prevent impurities from entering the lubrication mechanism. Frame-type oil seal cost is not high, the production process is not complicated, and the process is relatively mature, so it is widely used in all kinds of mining, metallurgy, environmental protection, vehicles, machine tools, ships, textile machinery, construction machinery, and so on.
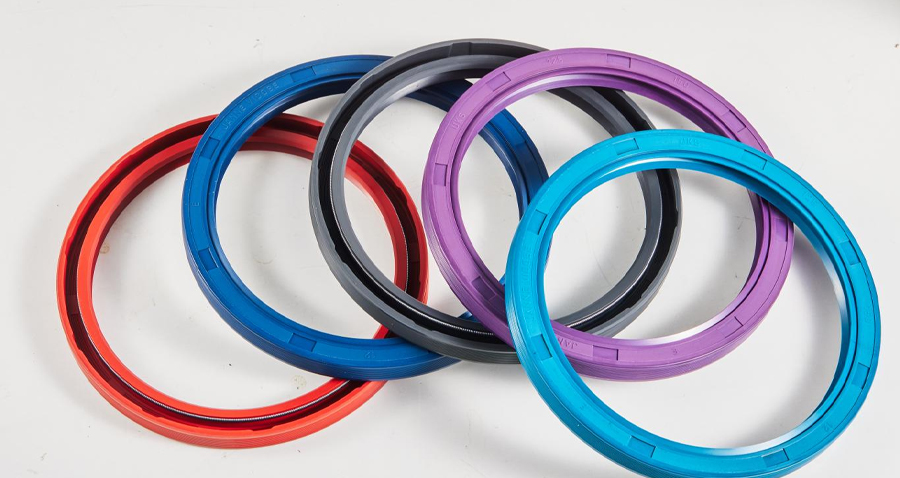
This article is mainly about installing the skeleton oil seal, so the structure selection, sealing principle, working characteristics, advantages and disadvantages, and material selection will be placed in other articles. At the same time, due to the diverse structure of the skeleton oil seal, we give an example of the most typical TCG double lip oil seal of the UKS brand in this paper.
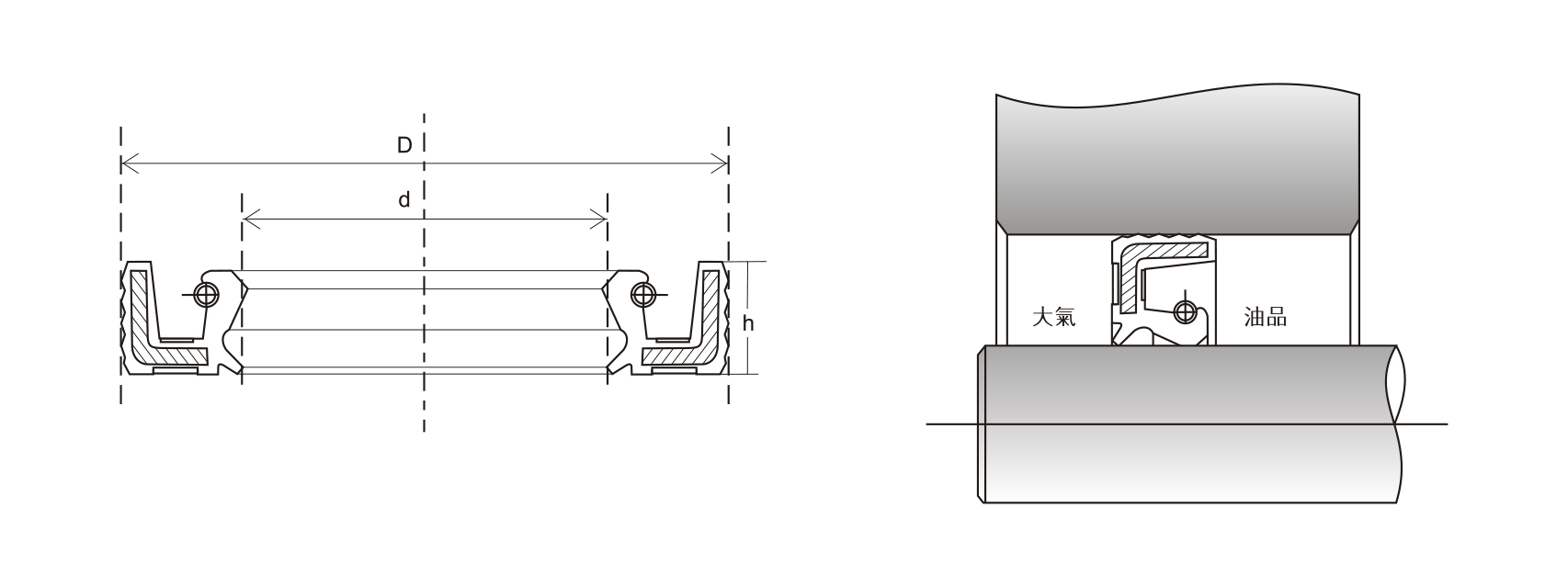
First, installation inspection and preparation
1. Read the assembly process requirements: if the company's technical department provides a standard process to guide the assembly of oil seals, please read the requirements carefully. Because the use environment and scene of the oil seal are different, the operation instructions of the process technology department play an important guiding role;
2. Check the size: check the diameter of the shaft and the diameter of the assembly hole, and check the specifications of the oil seal to determine whether it is completely matched;
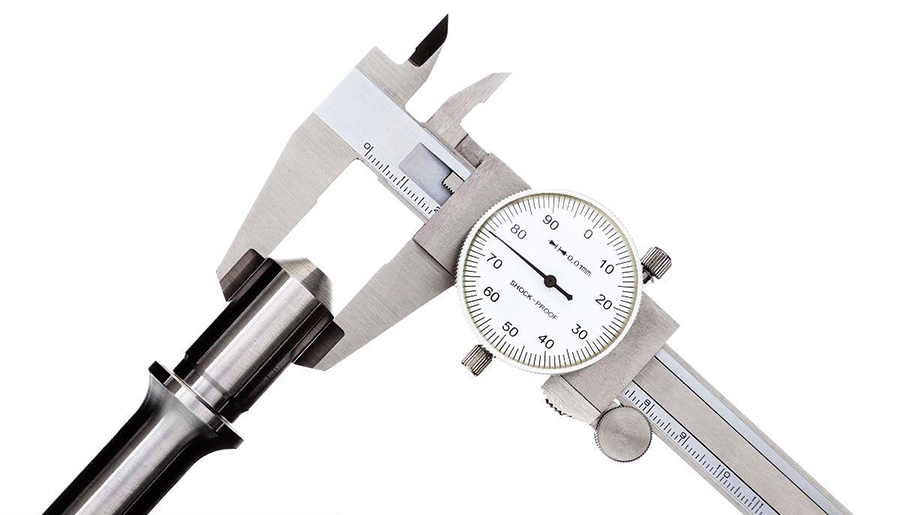
3. Check shaft, assembly hole, and chamfering: check whether the drive shaft and assembly hole have obvious turning and milling marks, and check whether the shaft and assembly hole have chamfering in line with the requirements
4. Check the cleanliness of burrs and assembly holes: check that the shaft and assembly holes have obvious burrs or sharp cutting edges, or rust, sand impurities, residual glue, oil, sand pores, structural defects, sand, iron filings, etc.
5. Check the quality and spring of the oil seal: check the main and secondary lip of the oil seal for defects, rubber particles, impurities, knife damage, rubber cracking, poor adhesion, spring off, spring open, eccentricity, oil seal circularity, oil seal deformation and so on;
6. If there is an oil return line, pay attention to the difference between forward (clockwise) and reverse (counterclockwise). The following is the type of oil return line (reflux pattern) [do not install the oil seal with reverse oil return line or reflux pattern] :
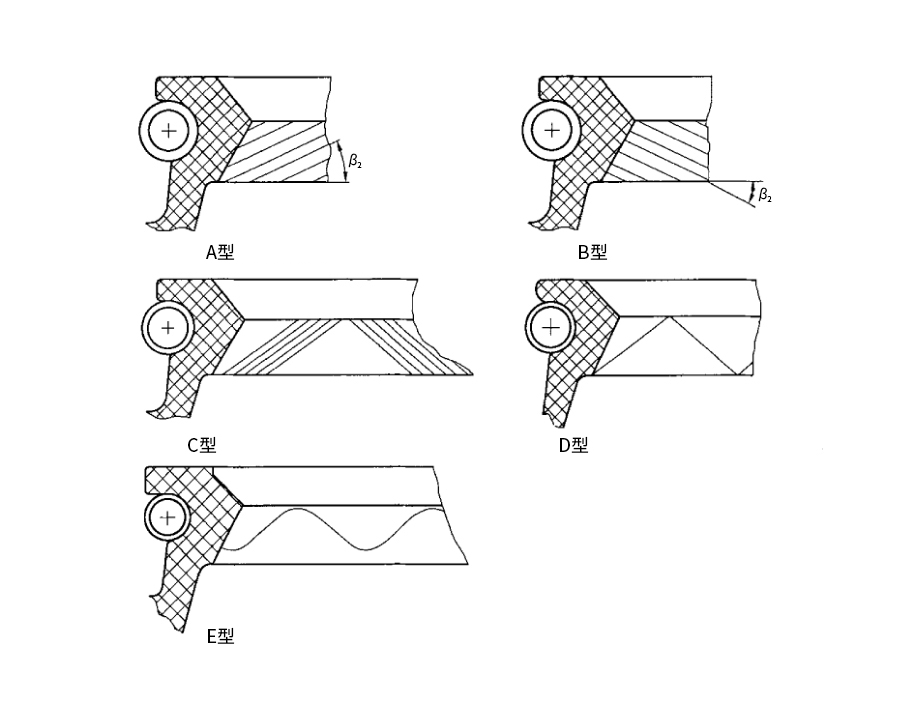
Ii. Precautions
1, Threads, holes, keyways, splines: some mechanical structure shafts will be milled with threads, holes, keyways, and splines, especially flat keyways and splines are more common. The above structure makes it very easy to damage the rubber lip of the oil seal during installation, so it must be fitted with a guide sleeve during installation to protect the lip of the oil seal from damage.
2, Thaft smoothness, assembly hole, hardness requirements:
The material of the shaft is recommended to be carbon steel, and when choosing cast iron material, try to choose ductile iron; The assembly hole material can be selected carbon steel or cast iron. If the aluminum alloy material is selected, please be sure to improve the processing accuracy and grease the installation, and pay attention to the difference in the thermal expansion coefficient of [aluminum alloy] to ensure that the mechanical operation at high temperature will not cause the skeleton oil seal to move or fall off due to the thermal expansion of the aluminum alloy assembly hole.
The diameter tolerance of the shaft shall not exceed H11 by the requirements of GB/T 1801-2009;
② The surface smoothness of the drive shaft according to the national GB/T 1031-2009 surface roughness machining accuracy requirements of Ra=0.2-0.63μm Rz=0.8-2.5μm;
③ The machining tolerance of the assembly hole shall not exceed H8 according to GB/T 1801-2009, and the machining roughness shall be Ra≤3.2μm and Rz≤12.5μm according to the requirements of GB/T 1031-2009.
④ Surface hardness of the drive shaft: Rockwell hardness HRC45~55 (high speed shaft hardness requirements > HRC55);
⑤ Surface hardness of the assembly hole: recommended Rockwell hardness HRC45;
Note: If there are special circumstances or special requirements, machining shaft, and assembly hole according to the requirements. If the shaft is made of copper or manganese, hard chromium plating is recommended.
3, The installation method
1, tool selection: hydraulic press, pneumatic press, lever pressure device, measuring tool, cushion plate, gear installer, rubber hammer, protective sleeve, guide sleeve, air tightness tester, oil seal disassembly special tools;
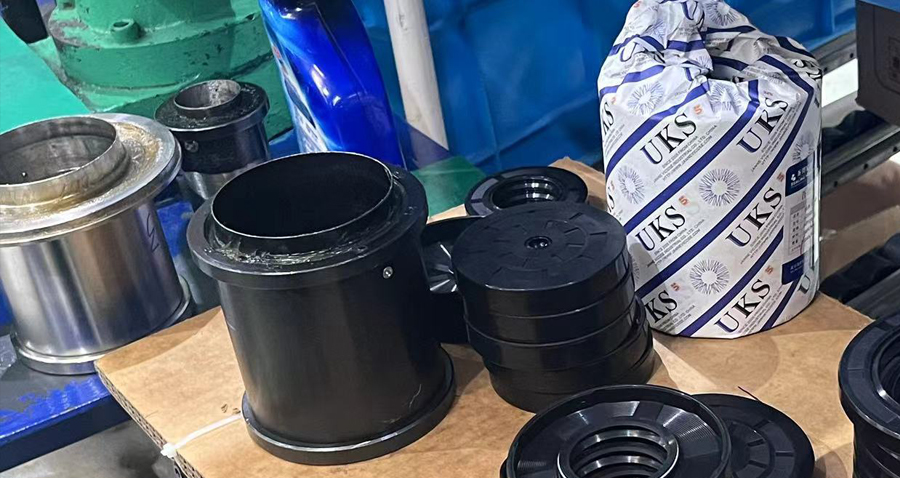
2, matching installation, chamfering to chamfering: To facilitate installation, the oil seal, drive shaft, and assembly hole are designed to guide chamfering, chamfering should meet the requirements of GB/T13871-2022 standard, to avoid the oil seal lip flip during installation, or the spring falls off.
Part chamfered drive shaft assembly hole oil seal α Angle oil seal θ2 Angle oil seal θ4 Angle oil seal β1 Angle
≥1mm 15-30° 15-25° 35-45° 30° 30° 15-45°
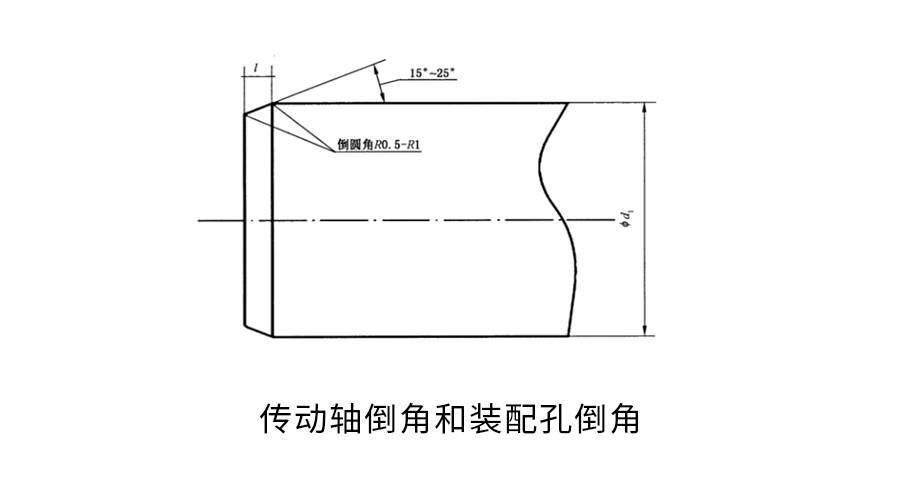
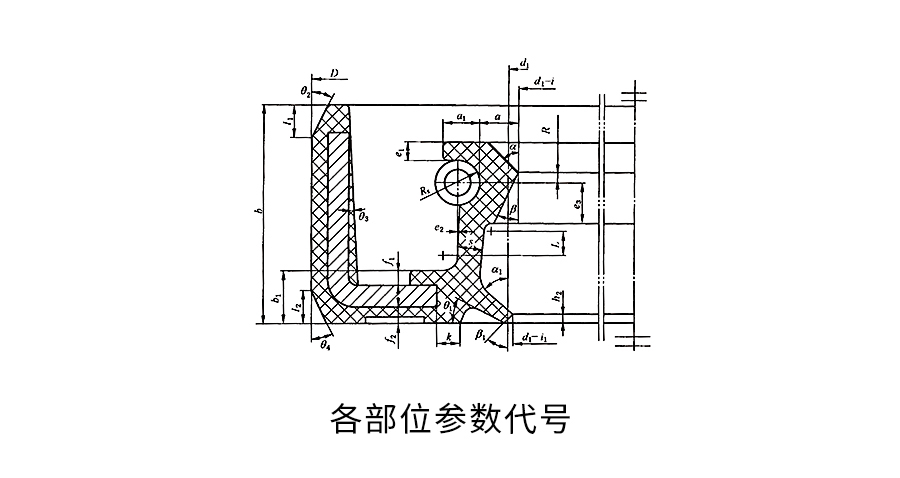
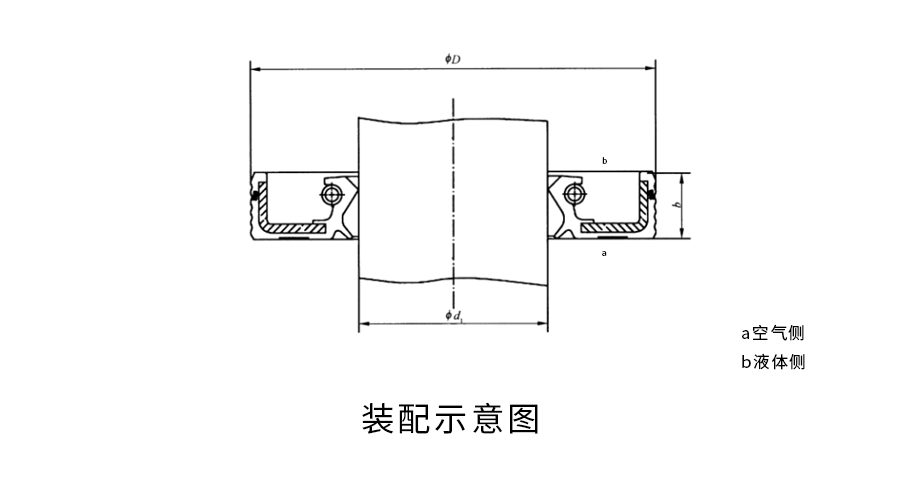
3, correct and wrong installation:
① Hydraulic press (air pressure machine) + fetal: this is a more common correct installation method, the uniform force of the hydraulic press so that the oil seal can be installed in place without damage, the installation speed of the press setting should be appropriately slow, can not be quickly installed to improve efficiency, which is easy to cause deformation and damage to the oil seal.
② Hydraulic press (air pressure machine) + plate: The force of the hydraulic press in the uniform distribution of the plate, can make the surface of the oil seal uniform force, and maintain a stable posture neatly installed into the groove structure.
(3) Hammer + pad: This installation method is also used by many installation masters, but there are several problems, one is the uneven weight of the hammer. Second, the force of the plate is not uniform. Third, the symmetry between the plate and the assembly hole is unstable. Improper operation is easy to spring off or oil seal eccentric operation.
Give an example
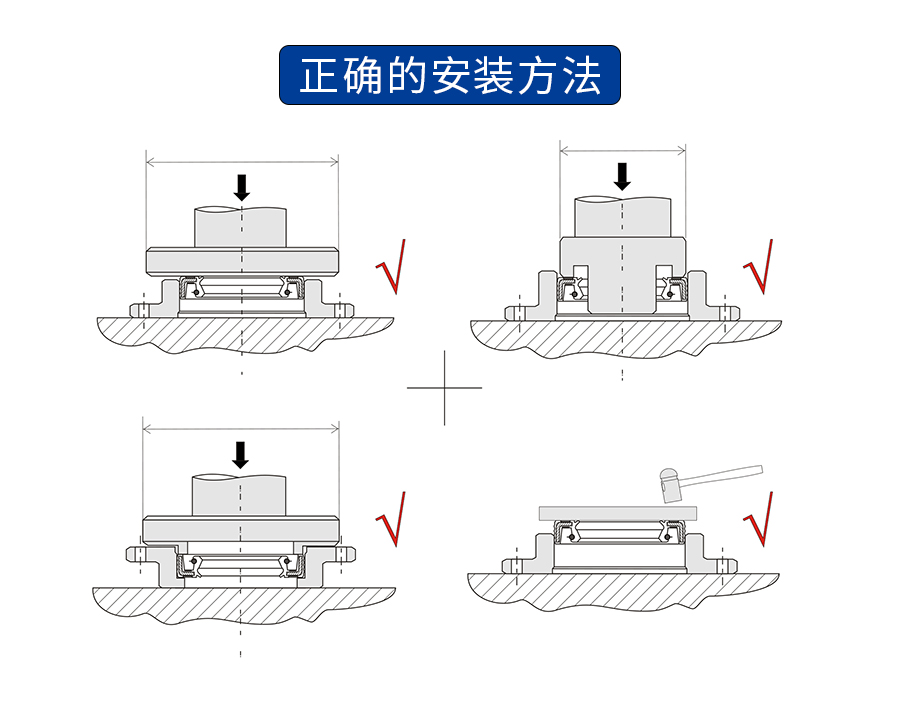
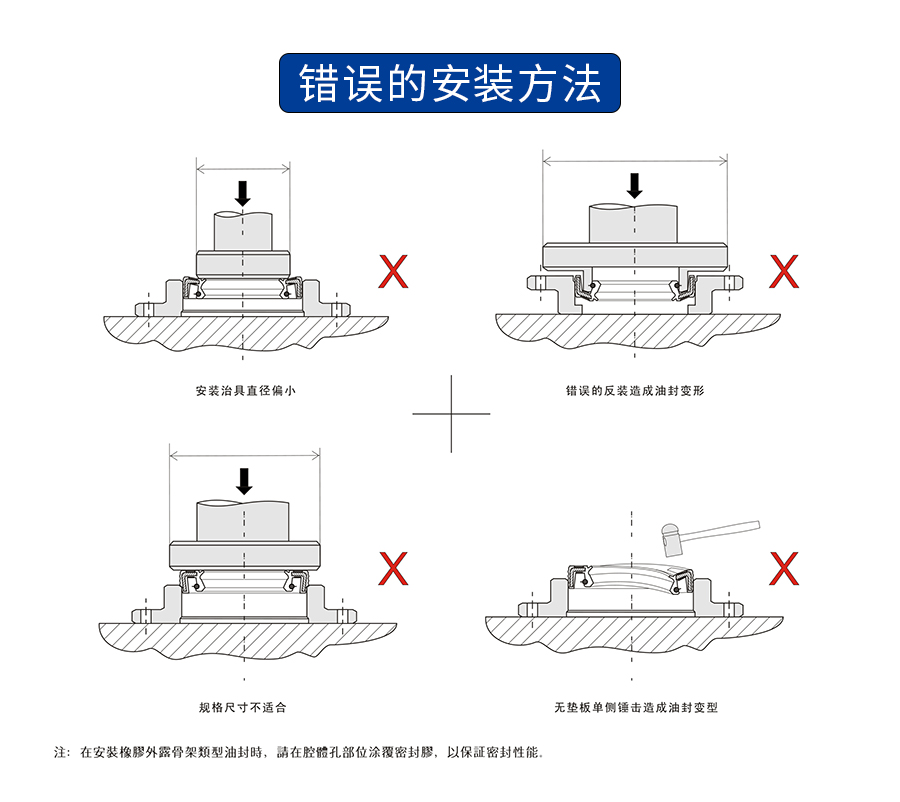
Four, installation direction
1, formal: most of the oil seals are formal, and [no special circumstances, only formal].
2, reverse loading: oil seal reverse loading is suitable for some special negative pressure environments, such as in wind turbines, building elevators, aerospace, Marine mining, mining, chemical, and other fields of some applications, that need to seal the negative pressure environment.
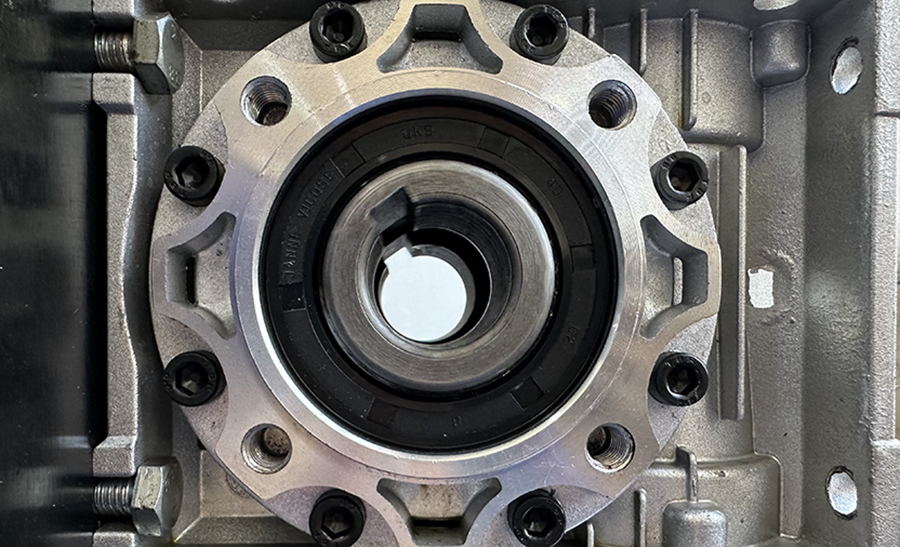
3, install the shaft first, and then install the hole: use the fixture to keep the shaft hole concentric as far as possible;
4, the remote end of the shaft: the shaft end should be equipped with a bullet head guide tool sleeve, as far as possible to avoid the spring is topped off;
Five, the selection and use of grease
1, the application of grease [must apply grease] : the installation of the drive shaft, the assembly hole must be lightly coated with grease, the outer diameter and lip of the oil seal should be thinly coated with grease, and the groove of the oil seal spring should be thickly coated with enough grease.
2. When applying grease, it is necessary to check that there is no anti-rust oil, no rust, no impurities, no iron filings, no sharp burrs, etc., if so, please clean it up;
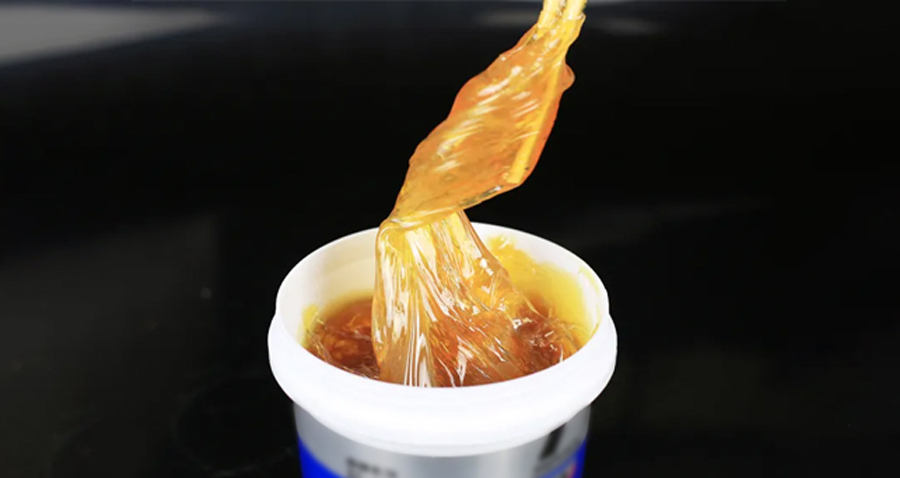
3, normal working temperature and grease selection: The use of nitrile skeleton oil seal temperature is generally below 120 ° C, the reasonable temperature should be within 80 ° C, too high a temperature will lead to premature aging of rubber. When using normal-temperature grease at high temperatures, the grease will liquefy and lose quickly, which will lead to the loss of lubrication of oil seals and bearings. Therefore, please choose a grease that can withstand high temperatures at high temperatures;
4. Auxiliary lubrication in the case of dry grinding: some motors, Roots fans, etc., have insufficient lubrication in many cases, and it is difficult to solve similar problems. Several solutions are recommended here: ① Seal a large amount of grease between the two oil seals of positive and negative mounting; (2) Grease the oil seal extensively, and add a padded pad with grease similar in size to the oil seal on the back; ③ Temperature resistant lithium grease containing molybdenum disulfide.
Vi. Installation anomalies and analysis
1, [spring drop]: the lip design is too thin, the spring arm is too small, the spring arm is too thin, the violent installation, the installation of different hearts, the reverse installation, the distal installation of the shaft, the oil seal inner diameter is too small, the installation speed is too fast without grease, the sleeve step is too large;
2, [lip flip]: oil seal inner diameter is small, distal shaft installation, installation of different hearts, lip is too soft, interference amount is too large, inner diameter size is not appropriate, β Angle bevel is not enough or β Angle is not appropriate;
3, [installation difficulties]: the size of the oil seal is inappropriate, the oil seal design structure is poor, the shaft and assembly hole lack chamfer, no grease, the oil seal trimming error does not θ2 or θ4 install supporting roles, the outside diameter is too large, the shaft and assembly hole surface is not smooth;
4, [oil capping bad]: distal shaft installation, oil seal inner diameter is not appropriate, installation of different hearts, fixtures are not appropriate, installation method is wrong;
5, [oil seal outer diameter degumming]: aluminum alloy assembly hole is not greased, skeleton and rubber bonding is poor, outer diameter is too large, assembly parts lack chamfer, outer diameter size is not appropriate;
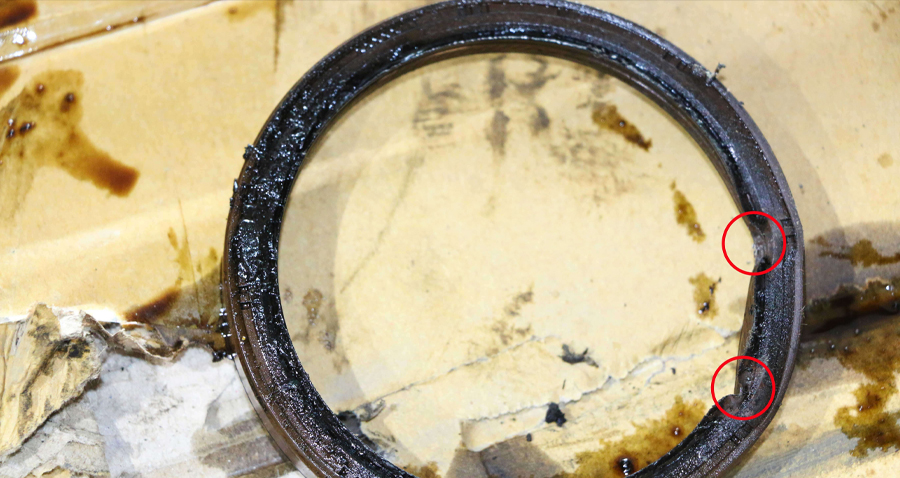
6, [lip rubber cut mark]: oil seal trimming knife injury, iron filings, sharp edge cutting injury;
7, [rubber tear]: there are keyway splines, iron filings, burrs and other foreign body bites caused by poor rubber vulcanization, oil seal tear, insufficient design thickness, or improper oil seal size;
8. [skeleton and rubber stripping]: poor adhesion between rubber and skeleton, installation without grease, oil seal outer diameter size is too large, or assembly hole tolerance is too small;
9. [After installation, it is found that there is a gap between the shaft and the oil seal]: the inner diameter of the oil seal is inappropriate, and the shaft size is incorrect;
10. [oil seal can be easily removed or floating after installation] : the oil seal size is inappropriate, the oil seal outer diameter is small or the assembly hole size is inappropriate;
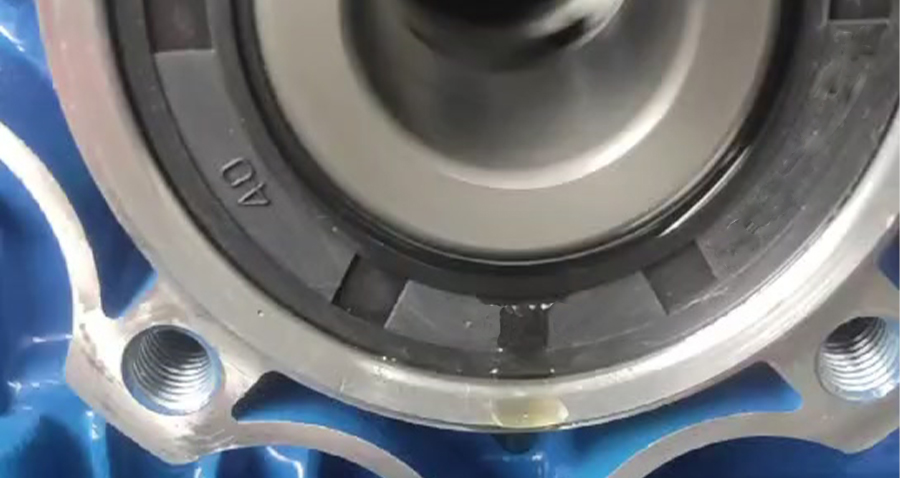
11. [oil seal tilt after installation]: The installation method is wrong, the oil seal is uneven, and the oil seal skeleton is defective;
12, [oil seal installation is not smooth]: the installation method is wrong, the oil seal bridge deformation, and the outer diameter is too large;
13, [oil seal skeleton fracture]: skeleton iron plate quality problems;
14. [oil seal deformation and distortion]: violent non-gasket hammer installation, lack of rigidity of oil seal skeleton, or insufficient skeleton thickness;
15, [influence power after installation]: the size of the oil seal is inappropriate, the shaft size is inappropriate, the lip design of the oil seal is unscientific, the grease is sticky, and the radial holding force of the oil seal is too large;
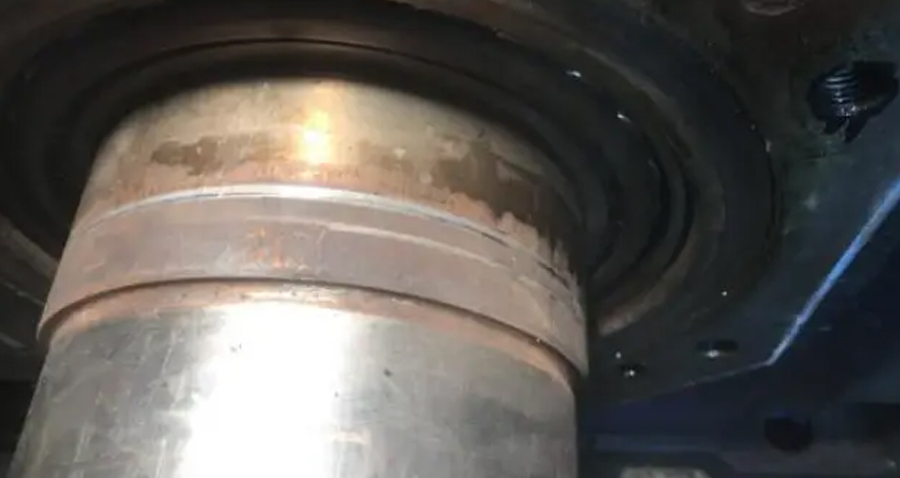
16, [running noise after installation] : no grease dry grinding, oil seal interference is too large, oil seal inner diameter is not suitable, oil seal lip structure design is poor;
17, [intermittent oil injection after installation]: different shaft holes, shaft bounce amplitude is too large, bearing imprecision clearance is too large, oil seal lip with shaft poor;
18, [drive shaft is worn out of the groove]: oil seal lip is too tight, shaft surface hardness is not enough, shaft surface roughness is poor, lack of lubrication;
19. [oil seal lip is squeezed] : oil seal inner diameter is too small, installation is incorrect, eccentric installation, shaft, and assembly holes are different hearts, oil seal inner and outer diameters are different, oil seal trimming is abnormal;
20, [oil seal spring break]: the spring interface is poor, the spring is too thin and overstretched;
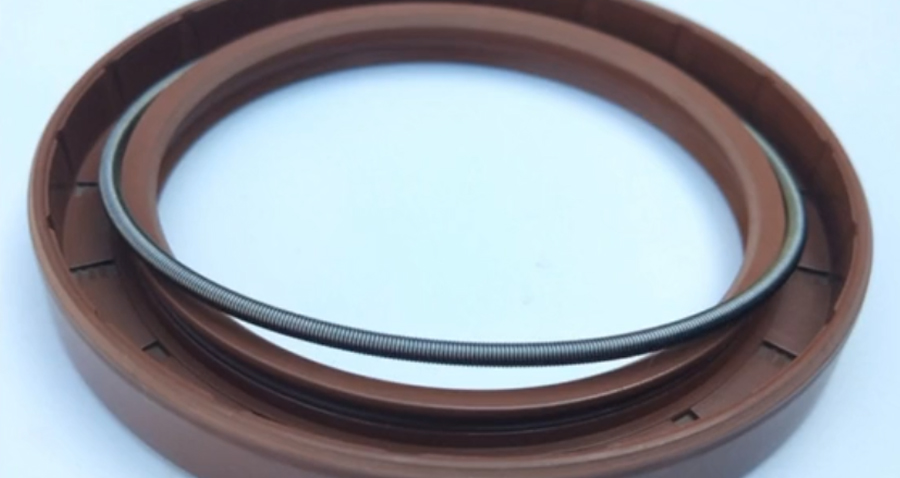
21, [oil leakage immediately after oil injection]: the size of the oil seal is inappropriate, the shaft or assembly hole has sand holes, improper installation, the oil seal has defects, the internal pressure is too large when the temperature rises and there is no pressure relief device;
22, [rubber expansion deformation after oil injection]: the selection of oil seal material error, oil quality problems, oil liquid pollution by other chemicals, oil selection error;
23. [oil seal cannot be installed in place] : the assembly hole is blocked by foreign bodies, the oil seal height is inappropriate, and the outer diameter of the oil seal is too large.
7. Inspection and verification after installation
With the continuous improvement of mechanical technology, to ensure the safer operation of mechanical transmission components, as the process guidance department of the enterprise, it is necessary to develop operation instructions. Assembly workers are required to do a series of inspections and verification work after the installation of the skeleton oil seal.
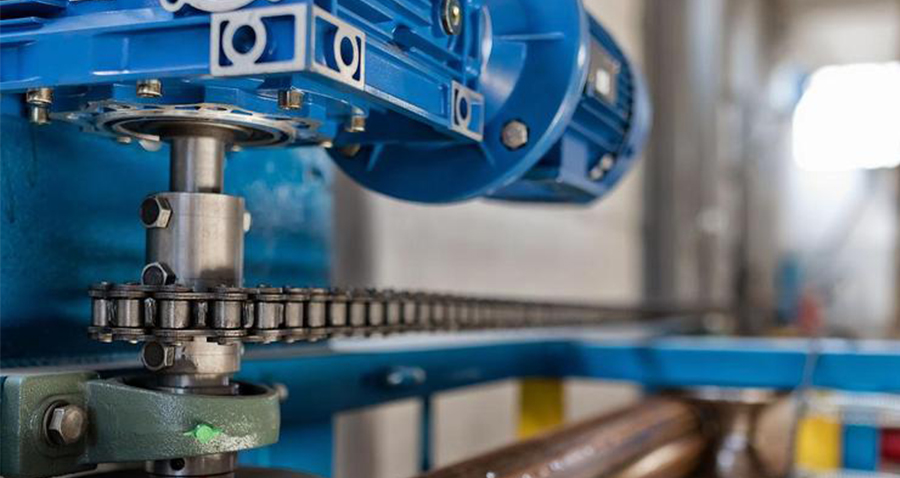
1. Avoid tilt: The inclined oil seal is not coaxial with the drive shaft and the assembly hole, which will produce high temperature, resulting in oil leakage or damage in advance;
2, avoid deformation: deformation of the oil seal will lead to oil leakage quickly when the lip of the oil seal rotates;
3, check whether the spring falls;
4, check whether the lip is flipped;
5, according to IP67/68 requirements to verify the sealing effect, the existing experience requires the production of a sealing device, positive pressure or negative pressure at 0.04MPa pressure for 30 seconds without leakage, is the seal qualified.